In the realm of high-performance engines, every component matters, and the materials used to create these components can make a significant difference in performance. This is particularly true for aftermarket pistons, which must withstand intense heat and pressure. This post will delve into the world of high-performance alloys used in aftermarket pistons, exploring their benefits, characteristics, and impact on engine performance.
Understanding Aftermarket Pistons
Aftermarket pistons are replacement parts not sourced from the vehicle’s original manufacturer. They’re typically employed in high-performance or racing applications, where they offer superior durability and improved performance over standard pistons. The material composition of these aftermarket pistons plays a crucial role in their function and performance, leading to the use of high-performance alloys.
High-Performance Alloys: An Overview
High-performance alloys in aftermarket pistons are specially formulated to provide optimal strength, heat resistance, and durability. These alloys often include elements such as aluminum, nickel, titanium, and even traces of precious metals like gold or platinum. Two of the most common high-performance alloys used in aftermarket pistons are forged aluminum and billet aluminum.
Forged Aluminum
Forged aluminum is a popular choice for high-performance pistons due to its exceptional strength and lightness. The forging process involves heating the aluminum and then applying high pressure to shape it, resulting in a denser and stronger material than cast aluminum.
Manufacturers like JE Pistons and Wiseco utilize 2618 and 4032 aluminum alloys in their forged pistons. The 2618 alloy, known for its excellent fatigue resistance, is ideal for high-performance, high-heat applications. The 4032 alloy, on the other hand, contains more silicon, reducing its thermal expansion rate and making it suitable for street performance applications where engine temperatures vary widely.
Billet Aluminum
Billet aluminum pistons are machined from a solid block of aluminum alloy, usually 2618. This method gives manufacturers complete control over the piston’s design and allows for intricate features that can’t be achieved with forging or casting. Billet pistons are typically used in top-tier racing applications where every ounce of performance matters.
The Impact of High-Performance Alloys on Engine Performance
The use of high-performance alloys in aftermarket pistons can significantly boost engine performance. These materials offer several benefits:
- Lightweight: High-performance alloys are lightweight, reducing the reciprocating mass in the engine. This results in quicker throttle response and higher RPM capabilities.
- Strength: These alloys are highly durable, capable of withstanding the intense pressures and high temperatures found in high-performance engines.
- Heat Dissipation: High-performance alloys are excellent at dissipating heat, which helps to prevent engine damage and prolong the lifespan of the pistons.
Reduced Friction: Some high-performance alloys, particularly those with added silicon, can reduce friction between the piston and cylinder wall, improving efficiency and power output.
Conclusion
In the world of aftermarket pistons, material truly does matter. High-performance alloys such as forged and billet aluminum provide the strength, durability, and thermal properties needed to withstand the rigors of high-performance and racing applications. As technology advances, we can expect to see continued innovations in high-performance alloys, offering even greater benefits for automotive enthusiasts and racers.
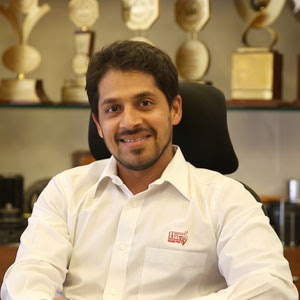
A top ranking student throughout, Akshay joined the family business right after graduation in 2006. After working for over 10 years in Agra Engineering Co, he decided to start his own company. Now as a partner in this new company he looks after business development and vendor management. A keen fitness enthusiast he tries new forms of exercise – crossfit, calisthenics, pilates, yoga and swimming. He’s an avid golfer as well – one of his many hobbies.